Who we are
Advanced Casting Technologies LLC (ACT) is the UAE’s first and only dedicated precision casting facility, formed as a strategic joint venture between Al Darmaki Group (UAE) and Microfound (Italy). Established under the Tawazun Economic Program, ACT brings European expertise and local vision together to elevate industrial capabilities in the UAE and wider GCC.
Our Mission
To transform the UAE’s industrial landscape by delivering superior casting solutions through World-class technology, quality, and performance.
Our Vision
To be the MENA region’s most advanced and trusted precision casting partner, empowering industries with local manufacturing excellence that meets and exceeds global standards.
Our Strategic Partner
The technological partner of ACT is a well-known brand in the field of precision casting and constitutes the starting backbone of the Company know-how. Based in Reggio Emilia, at the core of the Italian district of manufacturing excellency, Microfound boasts several decades of experience in the manufacturing of cast components for premium sectors such as motorsports, oil&gas, transport and fluid dynamics.
End-to-End Precision Casting Solutions
At ACT, we offer an integrated suite of precision casting services tailored for the world’s most demanding industries. Our capabilities span the full production lifecycle from engineering to prototyping, casting, finishing and testing.
Our processes are designed to meet exacting specifications and tight tolerances across aerospace, defence, energy, and medical applications.
By pairing the advantages of modern investment casting practice to cutting edge technologies such as 3D printing of wax models, we can provide both reliable cast-metal prototypes in few days, and big batches of parts, with the best-in-market cost effectiveness and quality.

Precision casting, also known as “Investment Casting,” or “Lost-wax precision casting,” is the perfect technology to obtain, with a single process, components with complex geometries and challenging mechanical properties in difficult-to-work materials, to eliminate mechanical machining and replace mechanical welding steps.
How to?
The process consists of creating a dedicated mould for each product, whose casting cavity represents the final shape and surface finishing of the desired component.
We build each mould by dipping a wax model of the component into a coating agent of creamy consistency, which will then solidify and become a thick refractory crust.
The wax is easily removed from the refractory shell, as it melts at a moderate temperature. At this point, the liquid metal is poured directly into the cavity, to form the part. The brittle crust is then broken to free the cast component.

Vacuum Investment Casting
Special steel components are mostly produced by conventional induction furnaces where the liquid metal could be partially exposed to the air, oxidizing some of its most sensitive elements.
Nevertheless, by employing Vacuum Induction Casting technology, ACT also produces special components made from nickel- and cobalt-based superalloys. The process enables the manufacturing of mission-critical parts that exhibit superior resistance to temperature, stress, and corrosion.
Our Vacuum furnace can process casting assemblies for equiaxed-grain metallurgy, with max dimensions of approx. 600 x 600mm and 80kg of cast weight (based on Ni alloy density)
Design & Co-Engineering
From the idea to the realization of the part: ACT is a partner that co-designs the component with the customer, so that the project can exploit all the potential of the precision casting process.
Our in-house team supports CAD development, casting simulation, and performance optimization before manufacturing begins.
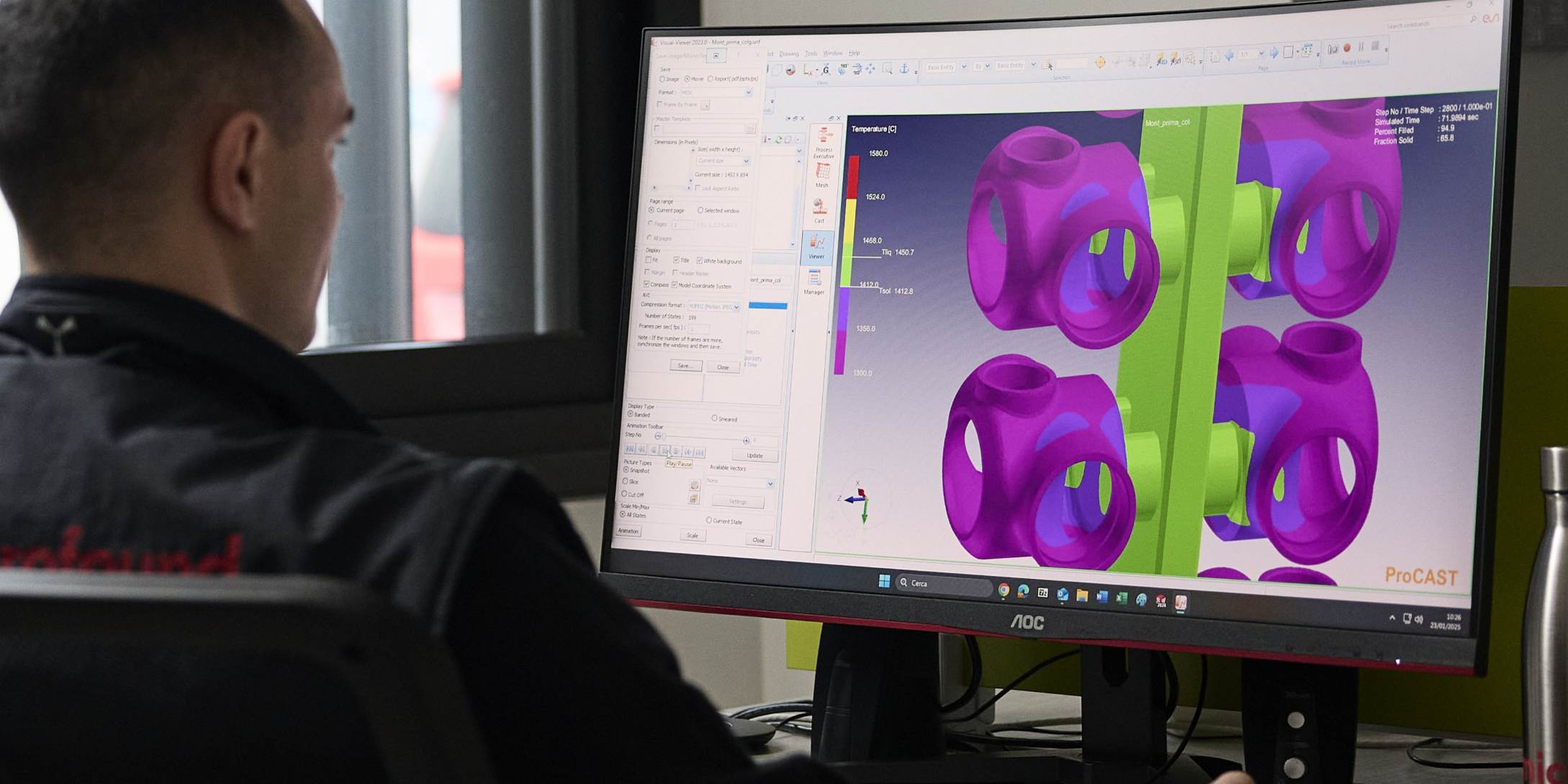
Rapid Prototyping
By leveraging 3D printing technologies to create sacrificial wax prototypes, all in all equivalents to those made by die-injection, we provide samples or pre-series cast components in record time. Therefore, we accelerate validation and time-to-market of our customers by skipping the traditional moulding work.
The cast prototypes produced in this way boast all the benefits of the casting process, both as metallurgical quality and mechanical properties
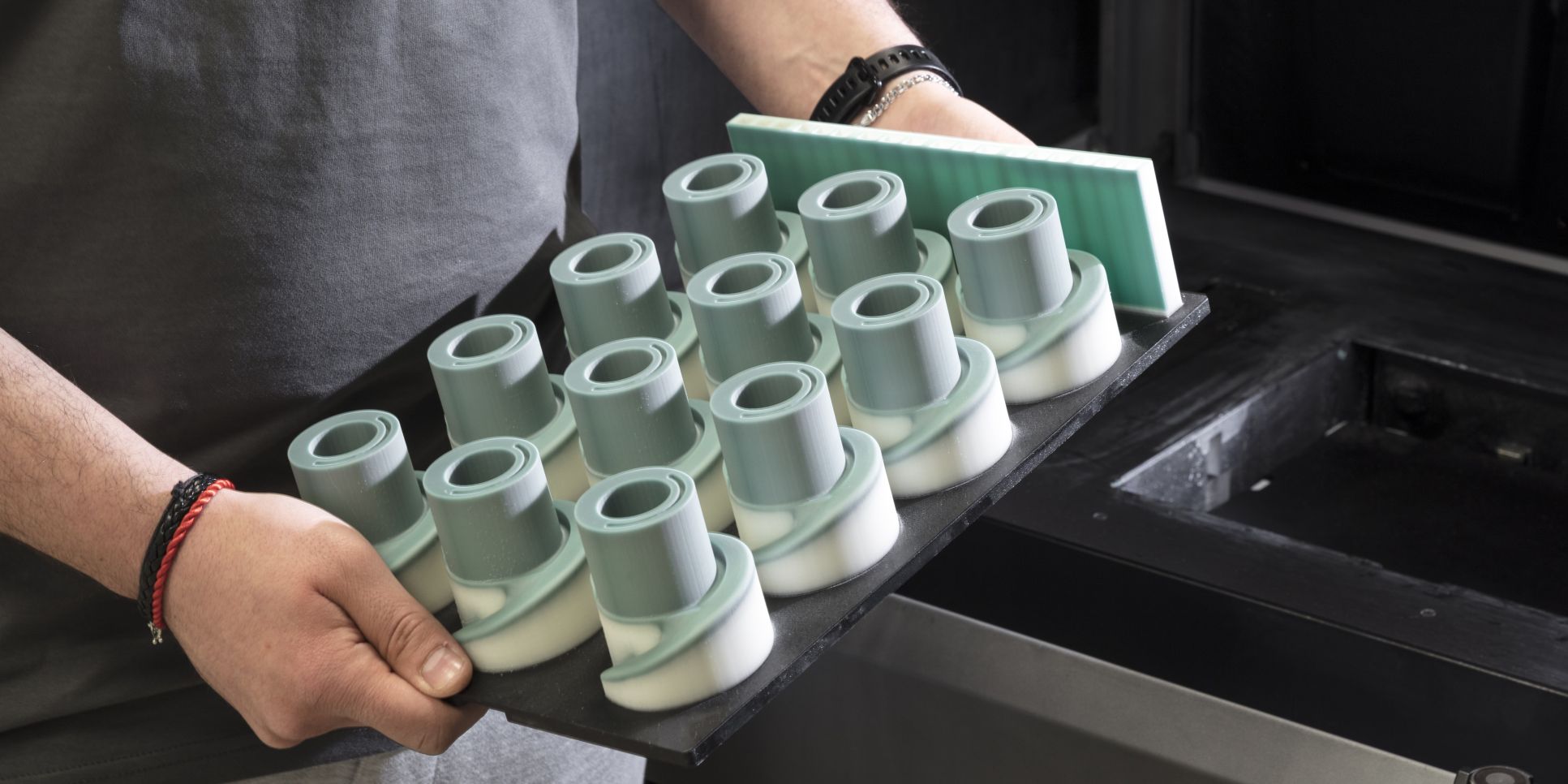
Quality control & Reverse Engineering
Our products are controlled with different degrees of accuracy, to meet the specified requirements of both geometrical tolerance and soundness.
Moreover, our 3D-scanning and CMM capabilities can also support us for projects of reverse engineering, such as to develop spare parts or upgrades for obsolete equipment.
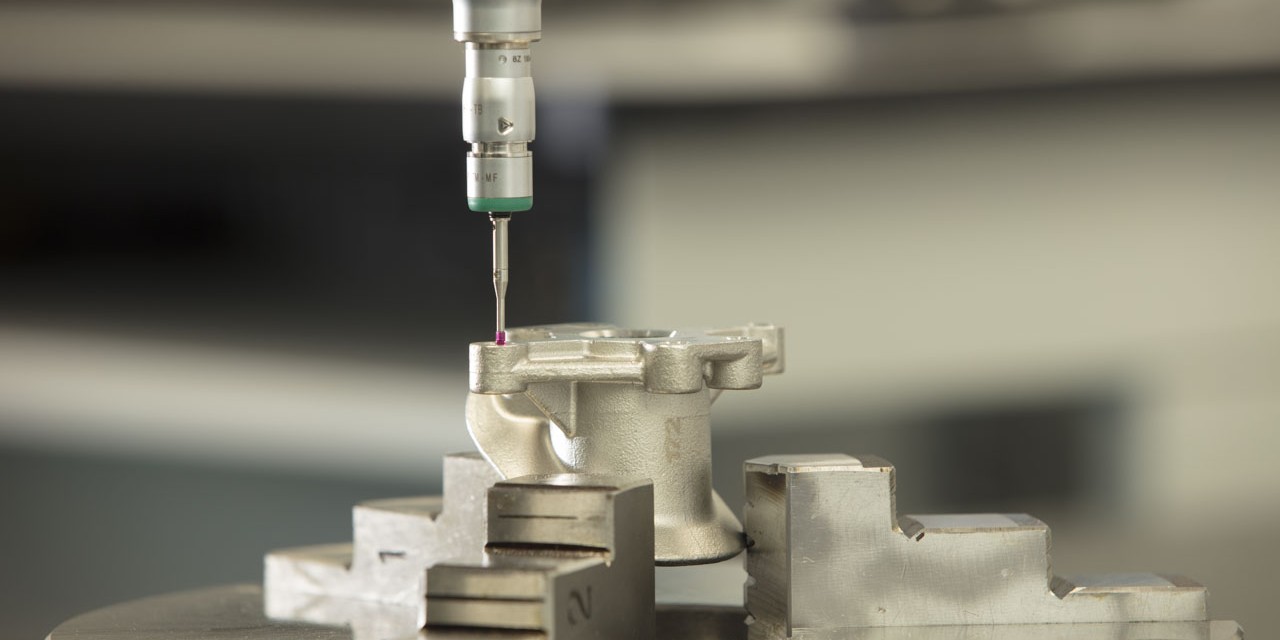
Machining &
Finishing
ACT delivers components ready for integration with full finishing services such as casting runners’ cutout, shot peening and deburring.
Our process ensures tight dimensional accuracy and optimal surface finish.
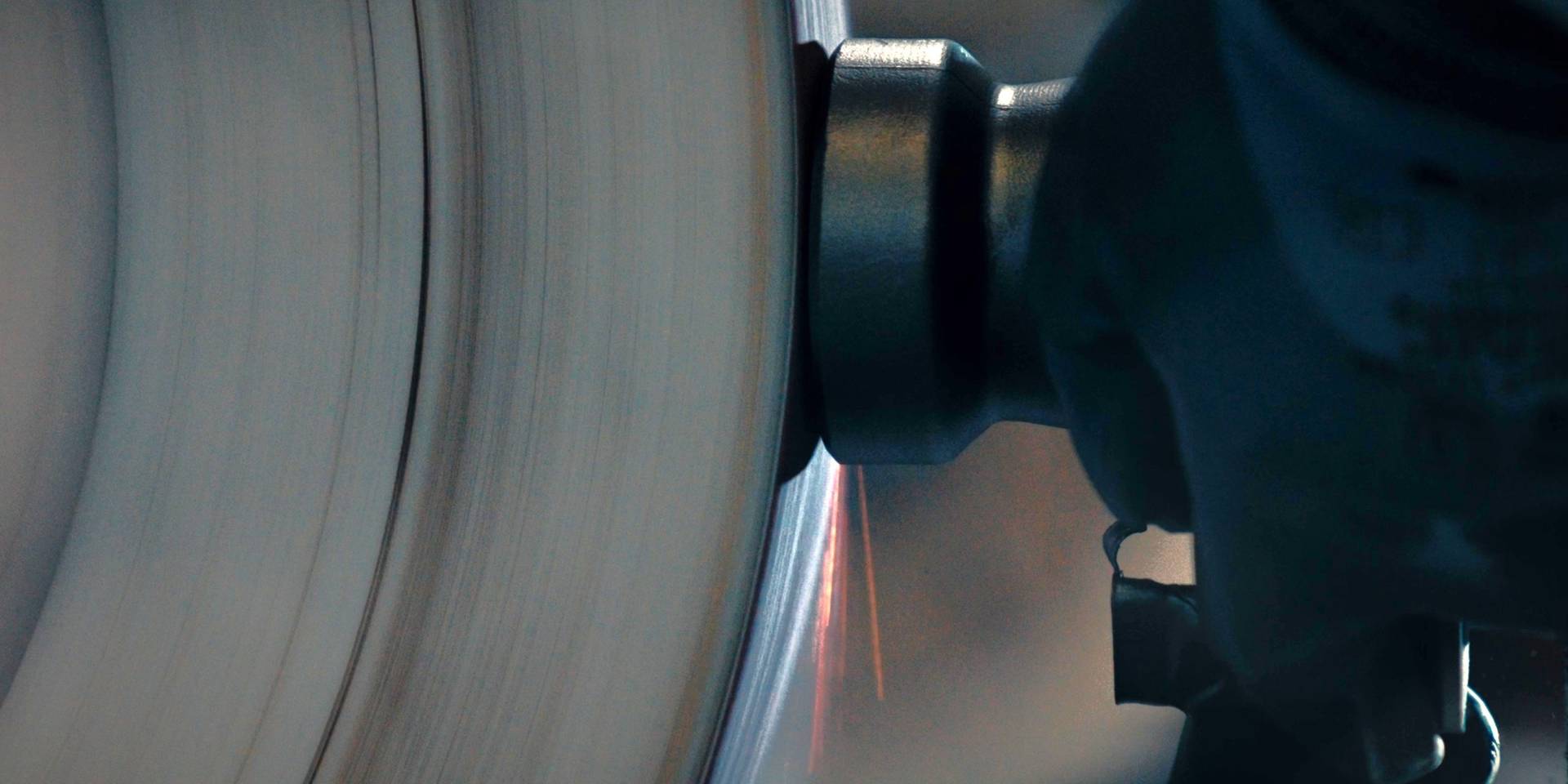
Materials
Expertise
Our material portfolio covers a full spectrum of carbon steels, special steels and superalloys including, but not limited to:
-Nickel and Cobalt-based superalloys (Inconel, Stellite…)
-Stainless Ferritic, Austenitic, Martensitic, Duplex, Precipitation Hardening
-Case hardening and Q&T steels
-Bearing and Tool steels (e.g. AISI5210 , AISI T1, M2 …)
Feel free to submit Your enquiries to info@adcastec.com
Industries We Serve
ACT provides critical components across all sectors where Performance,
Safety and Reliability are non-negotiable
Feel free to submit Your inquiries to info@adcastec.com
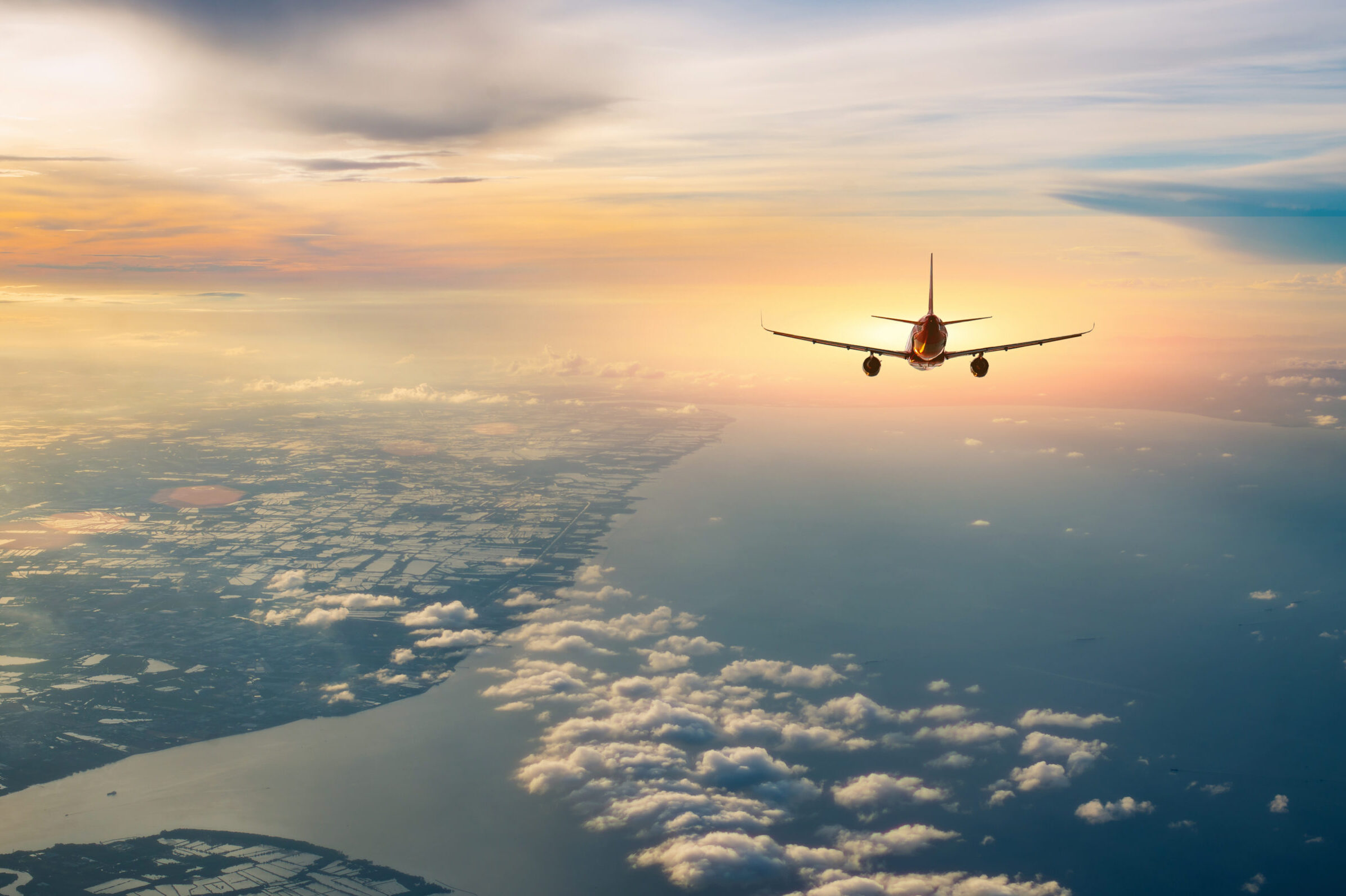
Aerospace
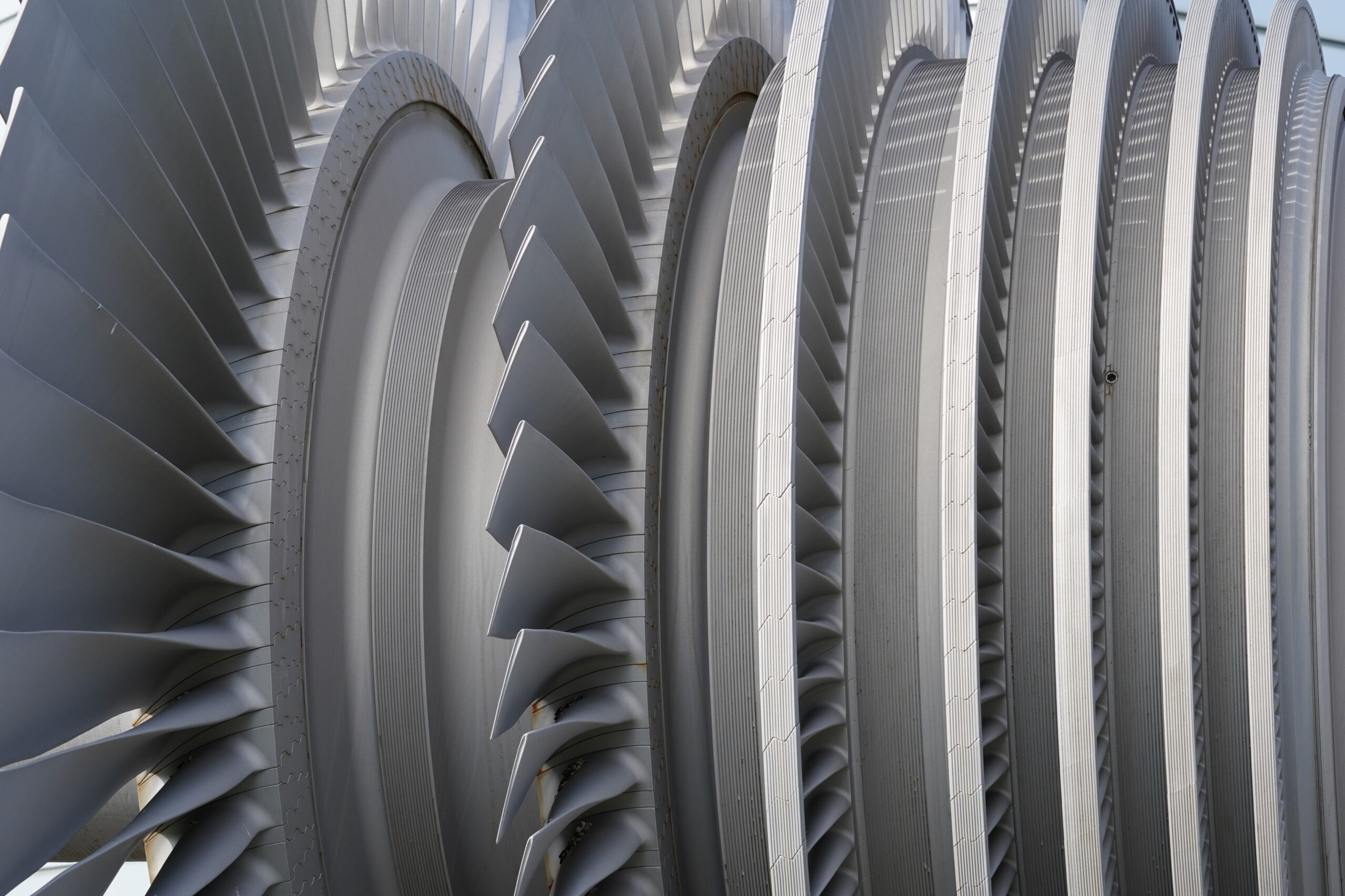
Power Generation
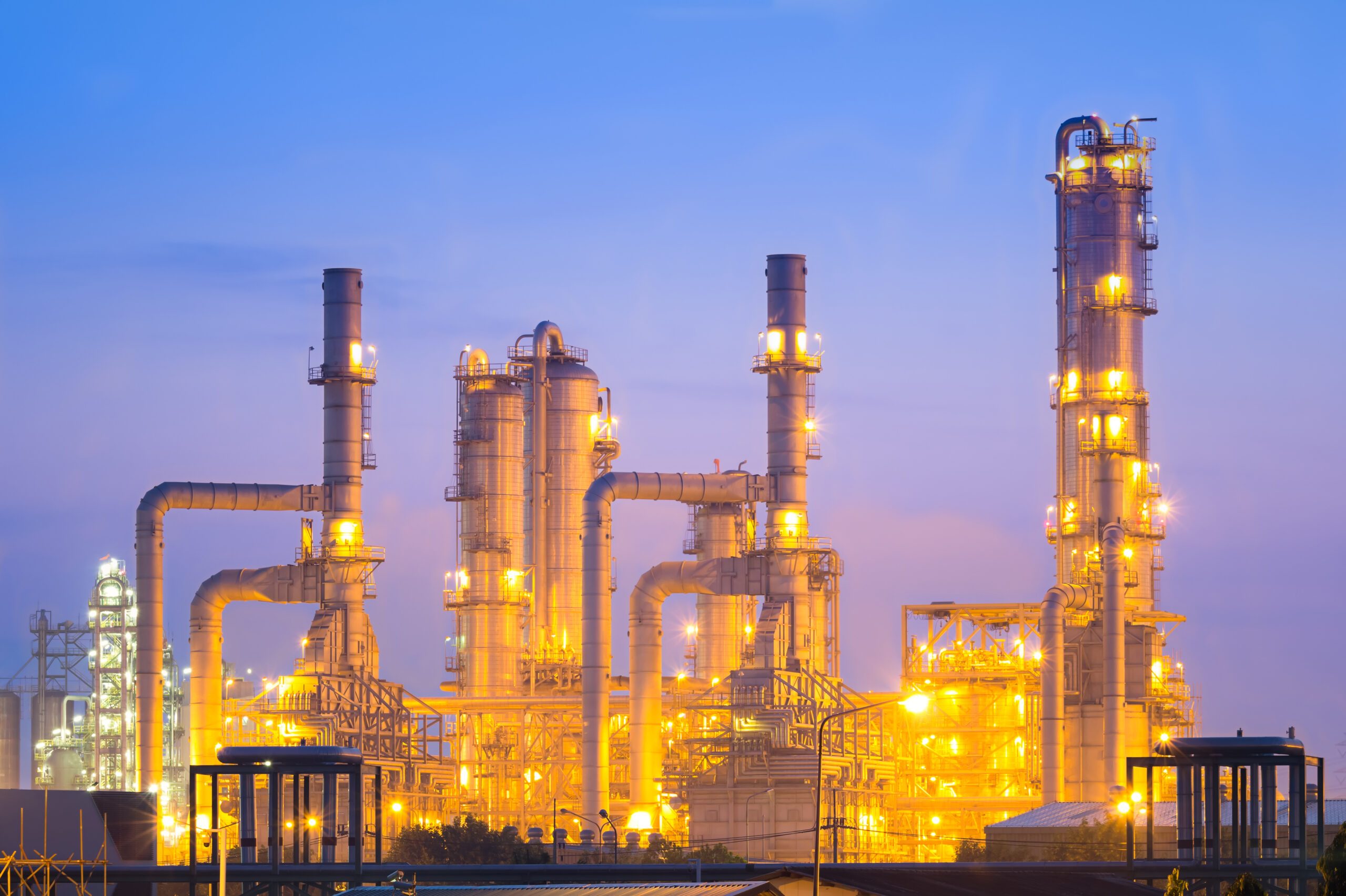
Oil and Gas
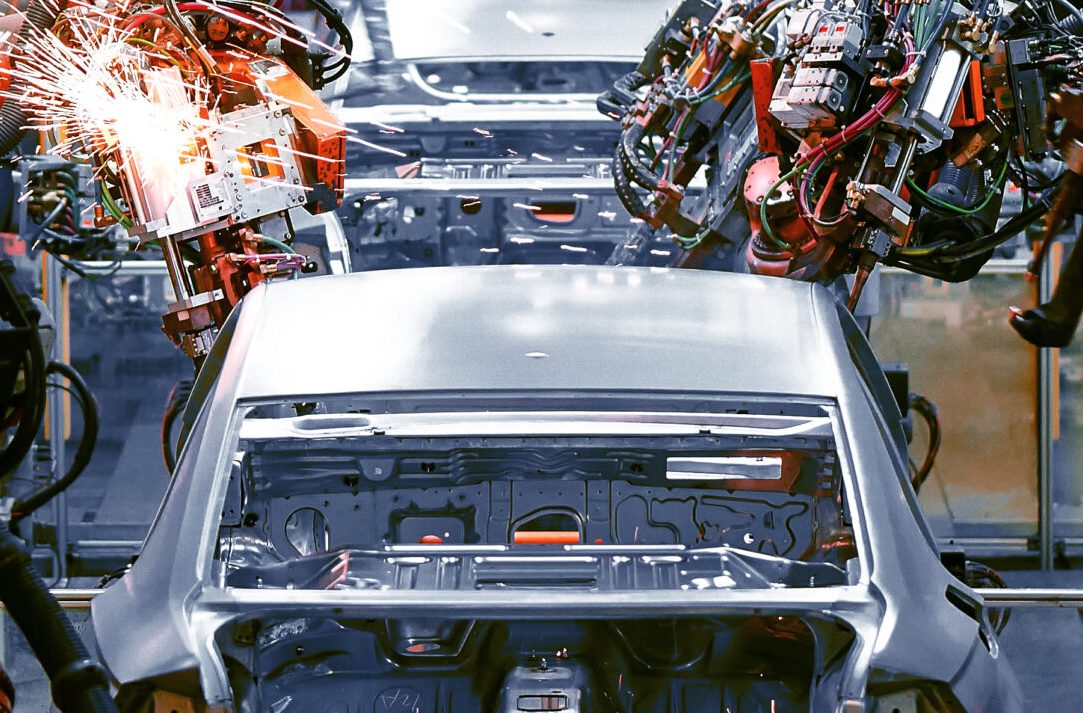
Automotive
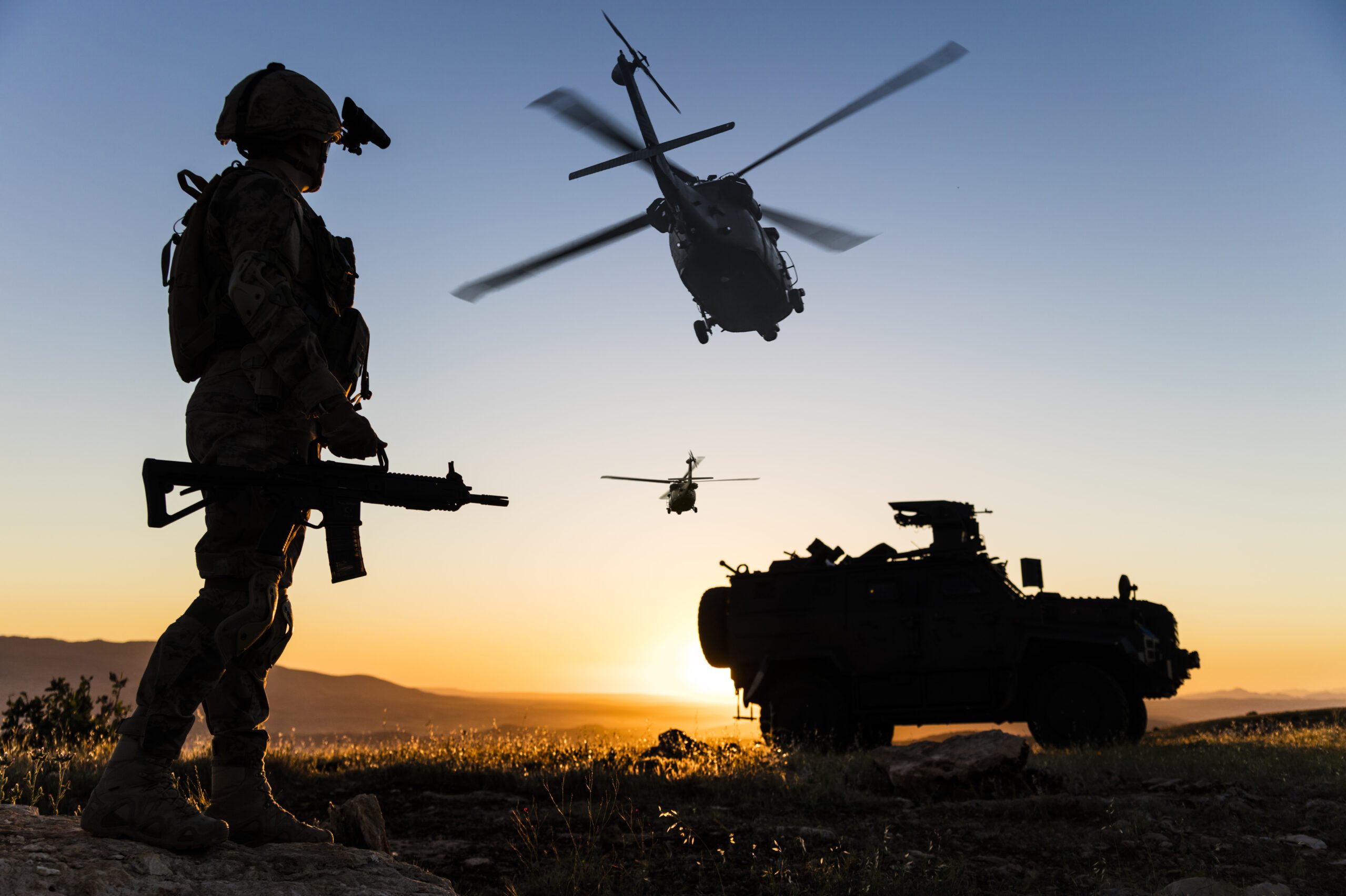
Defence
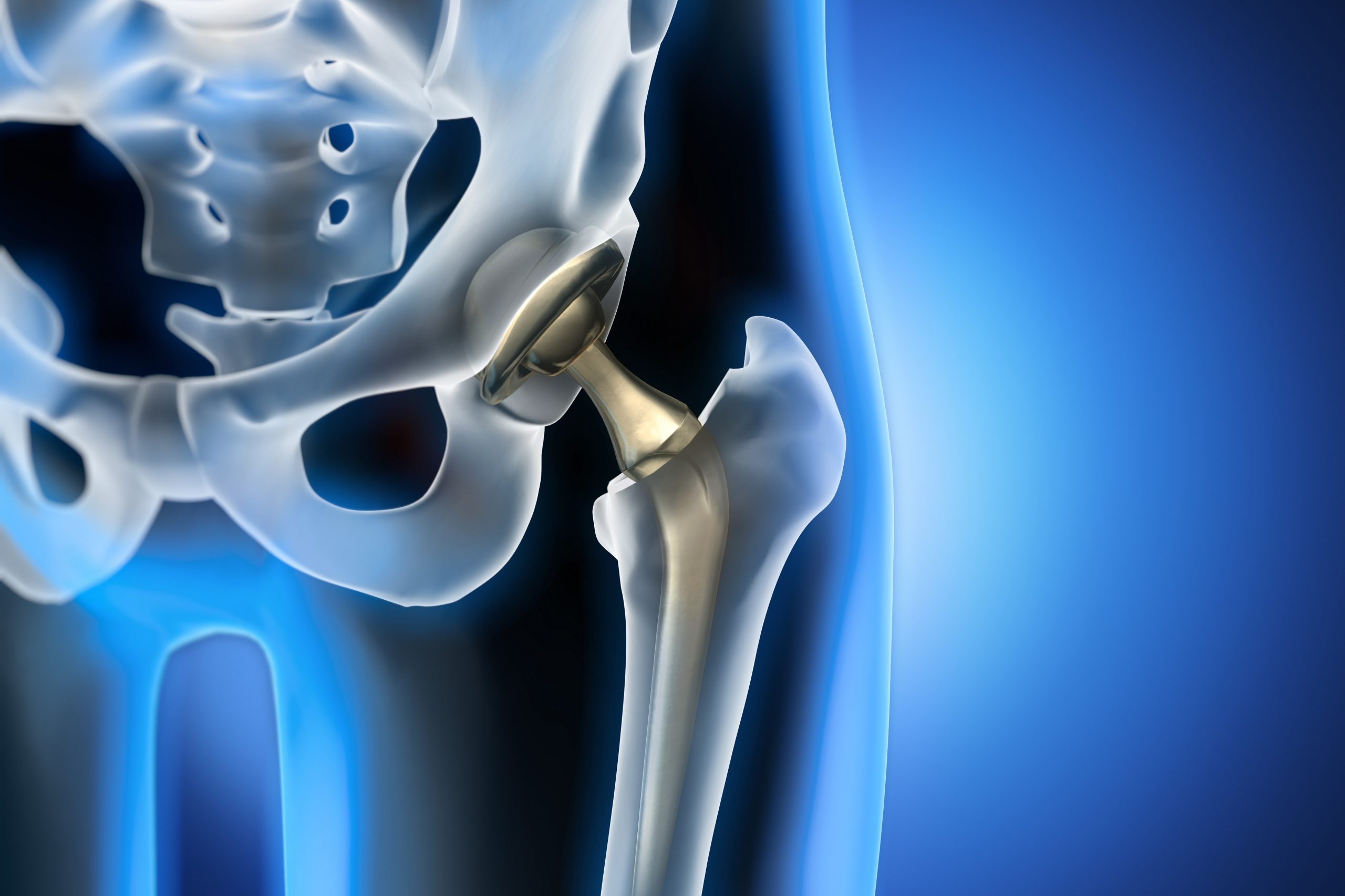
Medical
Our Facility
Located at Tawazun Industrial Park, Abu Dhabi ACT’s facility is meticulously engineered to meet the highest international standards for precision casting. The 4100 m² site features advanced environmental controls for temperature-sensitive areas like wax injection and shell coating.
The layout is optimized for end-to-end manufacturing—from digital simulation and pattern injection to melting, casting, finishing, and testing.
We are equipped to handle complex components across diverse sectors including aerospace, power generation, defense, healthcare, and oil & gas. With rapid prototyping capabilities, automated coating lines, vacuum and atmospheric melting technologies, ACT ensures scalable, repeatable, and reliable production for even the most demanding applications.
Our infrastructure enables:
• Flexible batch sizes and fast turnaround
• Consistent quality through process automation
• Reduced reliance on imports with localized production
• Integration of future technologies and expansion modules
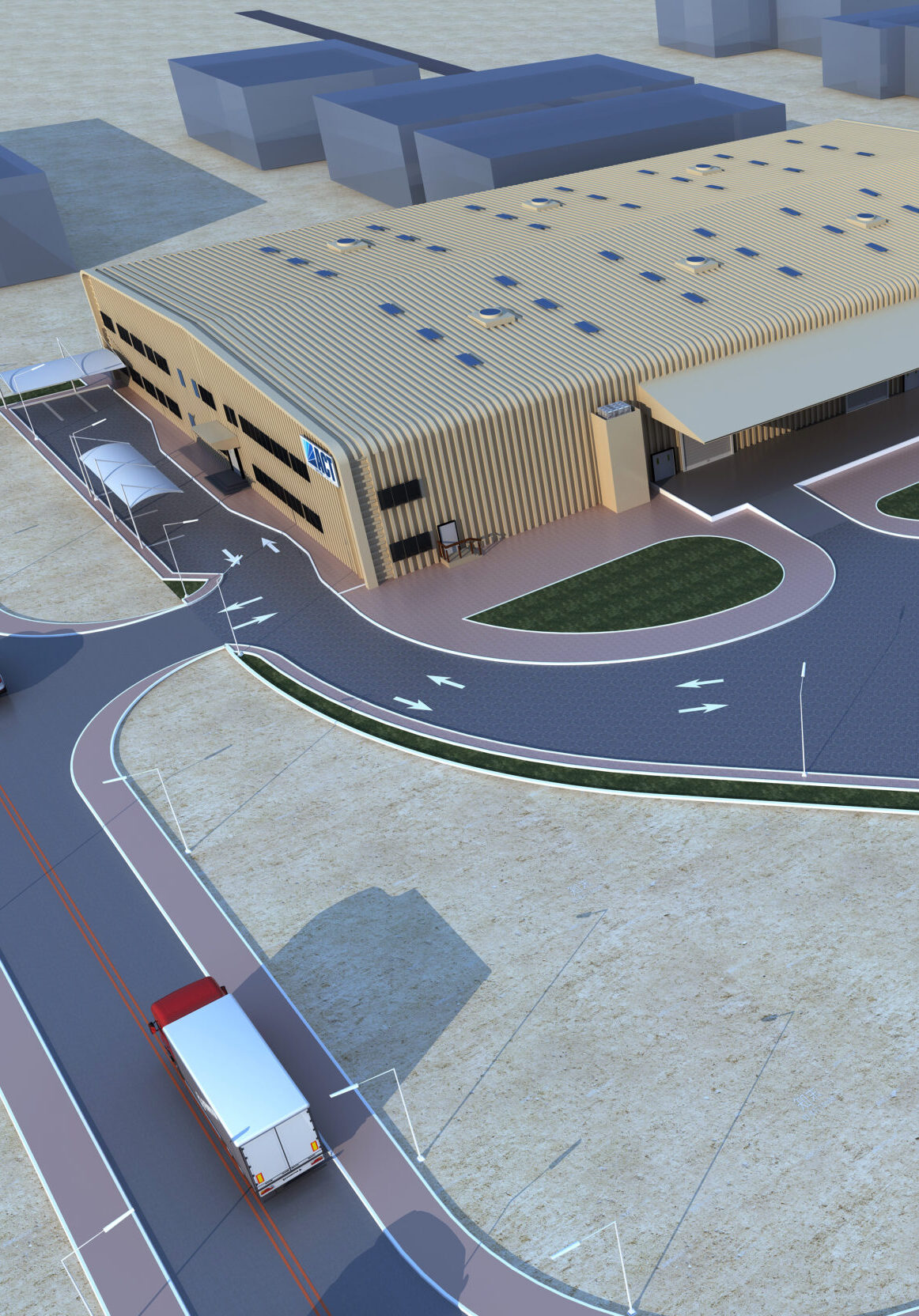
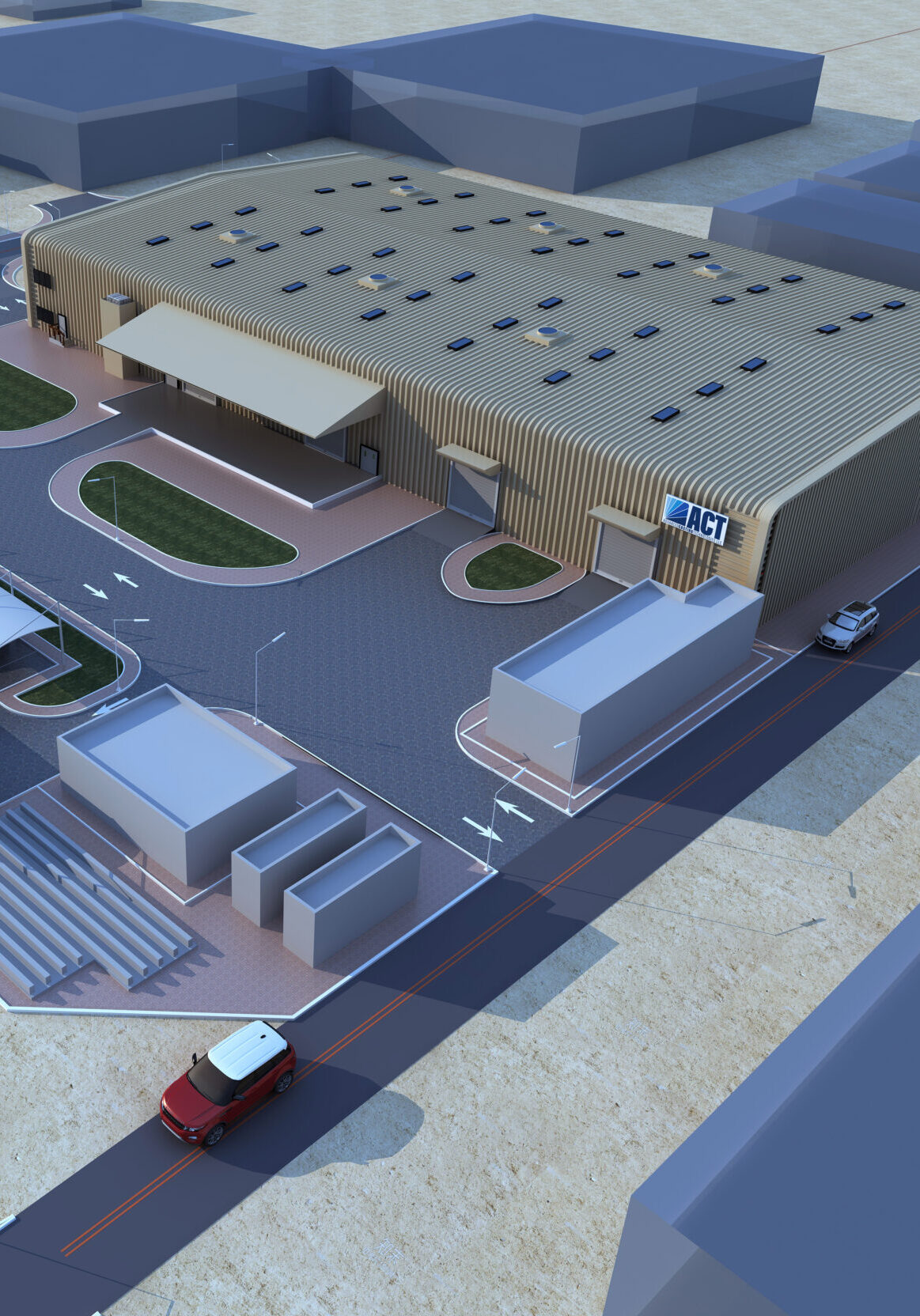
Contact us
Get in touch
Address:
Tawazun Industrial Park, Abu Dhabi S17 – PLOTS 24&25
Phone:
+971 2 621 2240
+971 54 478 4950